Air compressor shopping can be a daunting task; they are a staple in manufacturing and industrial processes and also account for a huge portion of your energy expenses. Throw in the countless compressor options that are on the market and you’ve got a recipe for decision paralysis!
While we can’t tell you exactly which air compressor will be the right one for you without investigating your operational needs, we can give you some tips and things to consider when you’re facing this major financial decision.
AIR QUALITY
You’ve heard the adage ‘quality matters’ and we agree whole heartedly with that sentiment.
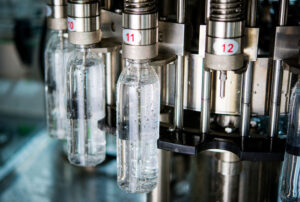
However, when it comes to compressed air, the end-air quality standard varies; a pharmaceutical manufacturer has a very different air quality standard than a textile mill.
That’s why you should always start by determining what quality of air you need. Jay Francis outlined these considerations exceptionally well in the article Air Quality Standards ISO 8573.1 & ISO12500 for Compressed Air Best Practices and we recommend skimming through the guidance there if you’re an air-quality newbie.
In a nutshell, the quality of air needed for your application may be dictated by:
(1) legal regulations (check out our article on Food Grade Lubricants here!) and/or
(2) the contaminants your application can or cannot tolerate.
It’s important to understand what kind of air you need before you can find a compressor that will get the job done.
POWER
A sister-part to differing quality requirements, understanding your air power requirements is critical. While Blake & Pendleton highly recommends a complete compressed air audit, there are a couple more things you can do to get an idea of your air consumption and needs.
- Log your compressor output. This is going to be key for those facilities who are already in full operation. How much CFM does your current system offer? Does it meet the current demand profile? Without an audit, this method can be misleading, but you can use it as a baseline to gauge your HP needs.
- Check the manufacturer specs for the equipment that will use your air. This is a great starting point when you aren’t sure how much air you actually need to operate your equipment and will save you a lot of time if you’re preparing to start from scratch.
APPLICATION
Your industrial application will specifically dictate the type of compressor that best suits your needs.
Oil free screw, oil flooded, and centrifugal compressors are the most common compressors in operation today.
The chart below is a good general reference for industry-compressor type match up.
Industry | Typical Compressor type |
Food & Beverage | Oil free screw |
Pharmaceutical | Oil free screw |
Automotive | Oil flooded screw, centrifugal |
Oil & Gas | Dependent, oil flooded screw |
Textile Mill | Oil flooded screw, centrifugal |
General plants | Oil flooded screw |
Electronics | Oil free screw
|
Plastics | Oil Flooded Screw |
Air quality, power requirements, and your application are all factors in play when you’re in the market for an air compressor.
While there are a few other things to consider (power source, design layout, environment) when you’re planning your compressed air system, the basic principles in this article will get you started if you’re in those early stages of determining which direction to go.
Finding the right compressor fit can be a challenge and Blake & Pendleton is here to help! Give us a call and we can help you navigate these options to set you up for a smooth operation!
To optimize your compressed air system and save on your energy expenses, ask us about a Compressed Air Audit!
References:
Francis, Jay. Air Quality Standards ISO 8573.1 & ISO12500. Compressed Air Best Practices, 2009. 2 May 2024.